Horváth & Partners can once again celebrate recognition for excellent project work: one of WirtschaftsWoche magazine's "Best of Consulting 2018" awards. The award went to a project in the Supply Chain Management category for the BMW Group and its supplier ZF Friedrichshafen AG. The award ceremony took place on November 20, 2018 in Düsseldorf. For yet another year, the consultancy firm is authorized to bear the “Best of Consulting Project Excellence” seal of quality. This is already the eighth award for the management consultants in the competition, which has existed since 2010.
The objective of the project was to strengthen the protection of the supply chains of the BMW Group and ZF Friedrichshafen by systematically identifying and reducing risks. The focus was on the supply chain for ZF's 8 HP eight-speed automatic transmission, which is installed in numerous BMW models. "Few automotive components are as complex as a modern automatic transmission. For some products, over 100 Tier-2 suppliers deliver a variety of components. If only one market participant fails to deliver, the transmission manufacturer's production and the supply chain of one or even several automobile companies could be seriously disrupted," explains Ralf Gaydoul, partner responsible for the automotive business at Horváth & Partners.
Tier-1 suppliers and OEMs therefore have an extraordinary interest in measures to prevent such incidents. This is precisely why the parties involved have set up a project to address this problem, together with Horváth & Partners. "The first step was to improve transparency across delivery levels and to develop a methodology to identify and evaluate risks in a comparable way," says Stefan Bultmann, responsible project manager at Horváth & Partners. Based on this, preventive measures should be designed first for those risks that pose the greatest threat to production and the supply chain.
The procedure considers several risk categories at the same time. In addition to natural disasters and fire, it also takes into account risks in production, logistics and IT, as well as strikes, political upheavals, financial bottlenecks and sabotage, which can pose a threat to the supply chain. The project participants weight these risks on the basis of three factors. In addition to 'occurrence' (i.e. probability), 'severity' and 'detection' are important indicators. Under 'severity' they classify the consequences for the entire supply chain, while 'detection' measures risk perception. The evaluation is weighted differently depending on whether the participant has already dealt with the risks and initiated countermeasures.
During site visits to ZF's plants in Saarbrücken and to 15 suppliers, these processes were tested and further refined. "The awareness of the importance of the topic was already high among all the suppliers visited and the feedback on the procedure was very positive. Every contact person reacted with an open mind," says Jörg Seibert, Project Manager at ZF. "Some had already swapped ideas with other suppliers." The project participants are expecting a positive kickstart for the future. Ideally, each supplier should approach its suppliers on its own initiative and suggest risk management according to the standards of the three project participants. This could form the basis for a new certification by the VDA (German Association of the Automotive Industry). In the medium term, the initiators want to involve further suppliers beyond the Tier 2 level. The goal is standardized risk management starting with the raw material supplier. "Such standardized risk management will become absolutely necessary in the future with ever more complex supply chains," says Bultmann.
Your Contact
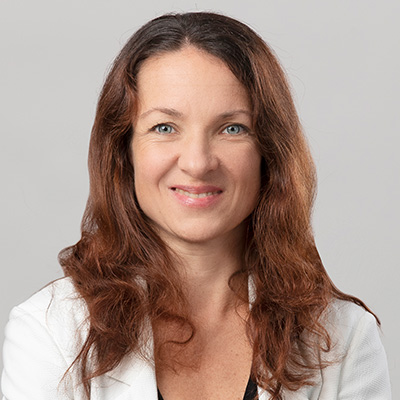
Juliana Tunsch